What is Porosity in Welding: Common Sources and Efficient Solutions
Wiki Article
Recognizing Porosity in Welding: Exploring Reasons, Impacts, and Avoidance Strategies
Porosity in welding is a persistent difficulty that can significantly influence the top quality and honesty of welds. As experts in the welding market are well mindful, comprehending the reasons, impacts, and avoidance methods related to porosity is essential for accomplishing durable and reputable welds. By delving right into the origin of porosity, examining its harmful impacts on weld high quality, and exploring effective prevention techniques, welders can improve their knowledge and skills to produce high-grade welds constantly. The detailed interplay of aspects adding to porosity requires a comprehensive understanding and an aggressive approach to guarantee effective welding end results.Common Sources Of Porosity
Contamination, in the kind of dust, oil, or corrosion on the welding surface area, produces gas pockets when heated up, leading to porosity in the weld. Improper securing takes place when the securing gas, generally made use of in processes like MIG and TIG welding, is unable to completely shield the liquified weld pool from reacting with the bordering air, resulting in gas entrapment and subsequent porosity. Additionally, insufficient gas protection, usually due to inaccurate flow rates or nozzle positioning, can leave parts of the weld unguarded, permitting porosity to form.Impacts on Weld High Quality
The presence of porosity in a weld can significantly jeopardize the overall quality and stability of the bonded joint. Porosity within a weld develops gaps or dental caries that compromise the framework, making it extra susceptible to breaking, corrosion, and mechanical failing.Furthermore, porosity can prevent the effectiveness of non-destructive screening (NDT) techniques, making it testing to discover other problems or interruptions within the weld. This can result in significant security concerns, especially in crucial applications where the structural integrity of the bonded parts is critical.

Avoidance Techniques Introduction
Offered the destructive effect of porosity on weld quality, effective prevention methods are crucial to maintaining the architectural honesty of welded joints. Additionally, selecting the proper welding parameters, such as voltage, existing, and take a trip speed, can aid lessen the threat of porosity development. By integrating these prevention techniques right into welding techniques, the event of porosity can be significantly reduced, leading to more powerful and extra trustworthy bonded joints.Value of Appropriate Protecting
Appropriate shielding in welding plays a critical role in preventing atmospheric contamination and guaranteeing the integrity of welded joints. Shielding gases, such as argon, helium, or a their website blend of both, are generally used to safeguard the weld swimming pool from reacting with elements airborne like oxygen and nitrogen. When these reactive aspects come right into call with the warm weld swimming pool, they can create porosity, causing weak welds with decreased mechanical homes.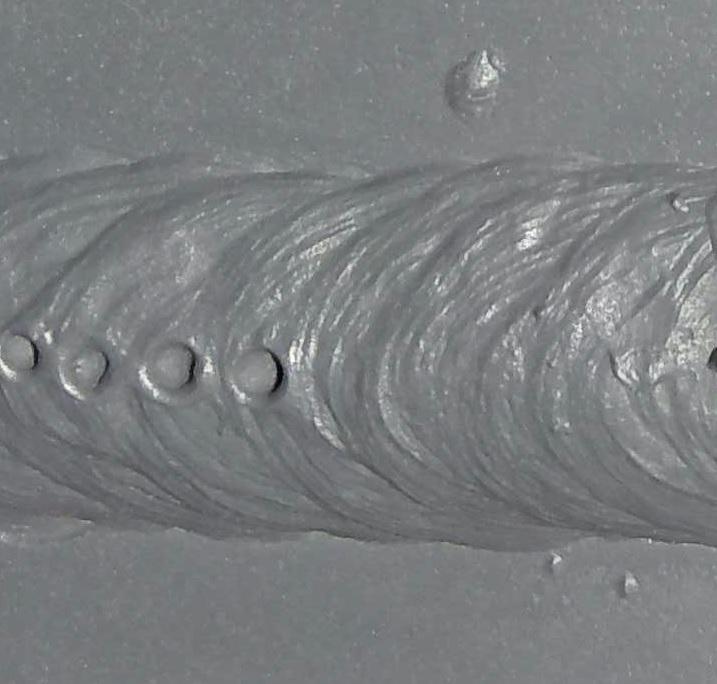
Insufficient protecting can lead to numerous defects like porosity, spatter, and oxidation, jeopardizing the structural honesty of the welded joint. Sticking to proper protecting methods is important to generate high-grade welds with minimal flaws and make certain the durability and integrity of the welded parts.
Tracking and Control Approaches
Just how can welders efficiently check and manage the welding process to ensure ideal results and protect against problems like porosity? By continuously checking these variables, welders can recognize deviations from the suitable problems and make immediate changes to prevent porosity formation.
In addition, applying correct training programs for welders is essential for monitoring and controlling the welding process efficiently. What is Porosity. Informing welders on the value of maintaining regular criteria, such as proper gas shielding and take a trip rate, can aid prevent porosity problems. Regular evaluations and accreditations can additionally make sure that welders excel in monitoring and regulating welding processes
Moreover, making use of automated welding systems can improve monitoring and control abilities. These systems can precisely control welding specifications, decreasing the likelihood of human mistake and making certain constant weld quality. By integrating advanced monitoring innovations, training programs, and automated systems, welders can successfully keep track of and regulate the welding procedure to minimize porosity problems and attain high-grade welds.
Conclusion

Report this wiki page